Understanding the Role of a Mold Manufacturer in Modern Industry
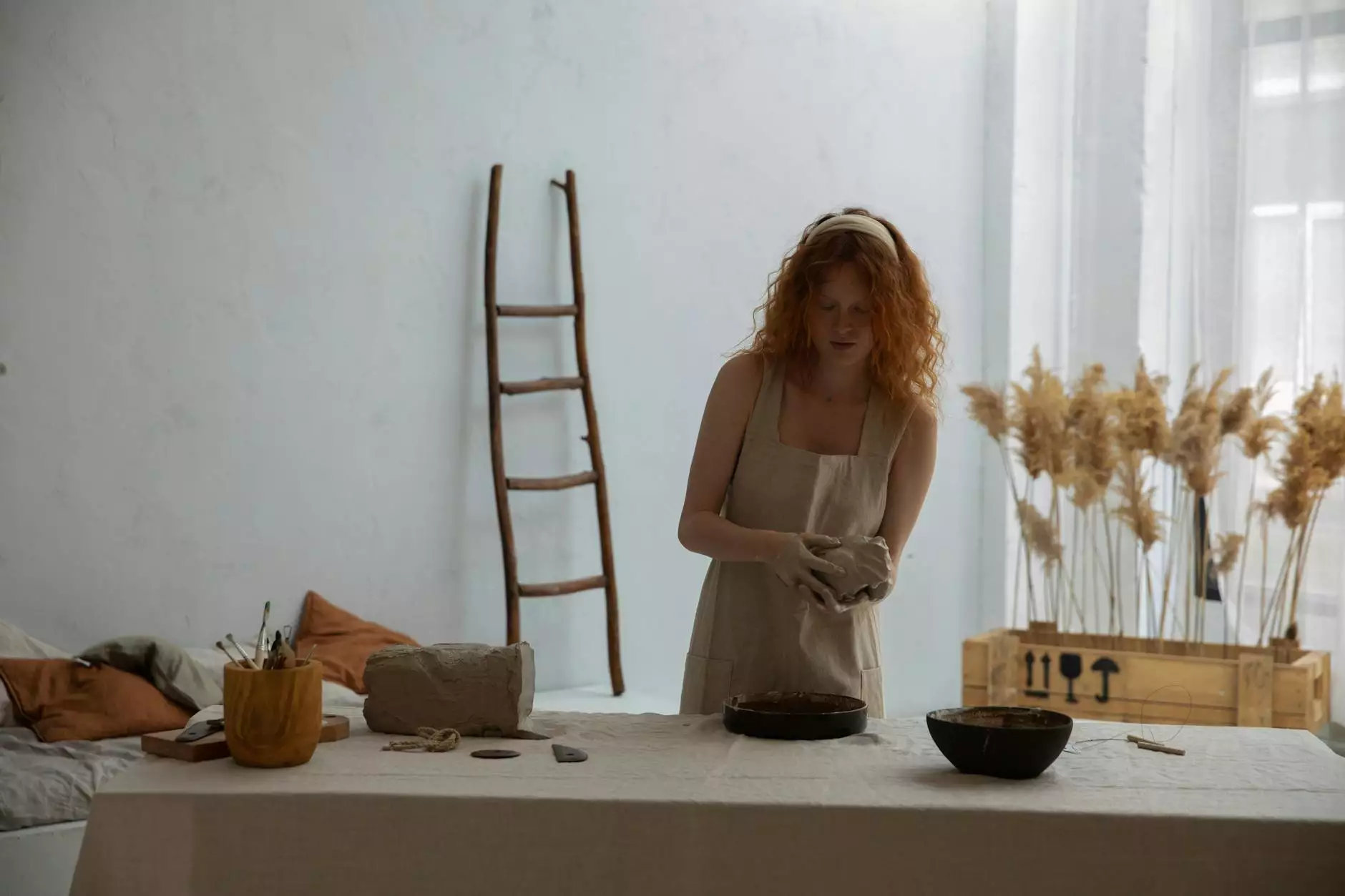
The phrase "mold manufacturer" encapsulates a pivotal sector within the vast landscape of manufacturing. As industries continue to evolve and machinery technology advances, the importance of mold manufacturers becomes increasingly evident. This article delves into the multifaceted world of mold manufacturing, examining the processes, benefits, and applications that mold manufacturers, like deepmould.net, provide.
What is a Mold Manufacturer?
A mold manufacturer specializes in the design and fabrication of molds used for shaping materials such as metals, plastics, and composites. Their expertise lies in creating tools that perform as the foundation for mass production, directly impacting the quality, efficiency, and cost-effectiveness of manufactured goods.
The Importance of Molding in Manufacturing
Molding is a critical process in various industries, from automotive to consumer goods. Here are several key reasons why mold manufacturing is vital:
- Precision Engineering: Mold manufacturers utilize advanced technologies to create molds that ensure products are manufactured with precise specifications.
- Cost Efficiency: High-quality molds reduce waste and enhance production speed, making the overall manufacturing process more cost-effective.
- Innovation: Mold manufacturers are at the forefront of innovation, developing new techniques and materials that push the limits of design and functionality.
- Scalability: Effective mold design allows for scalability in production, enabling brands to meet varying market demands without compromising quality.
The Mold Manufacturing Process
The process of mold manufacturing consists of several key stages:
1. Design and Prototyping
The initial step in mold manufacturing is the design stage, which involves creating detailed specifications based on client needs. Advanced Computer-Aided Design (CAD) software is often used to produce 3D prototypes. This allows manufacturers to visualize the mold before actual production, ensuring accuracy and functionality.
2. Material Selection
Choosing the right materials for mold making is crucial. Common materials include:
- Steel: Renowned for its durability, steel molds are typically used for high-volume production.
- Aluminum: Lighter than steel, aluminum molds are favored for their quicker turnaround times during prototyping.
- Composite Materials: Offering a balance between cost and performance, composite materials are becoming more popular in certain applications.
3. Machining and Fabrication
Once the design is finalized and materials are selected, the machining process begins. This involves:
- CNC Machining: Computer Numerical Control (CNC) machines provide high precision in cutting and shaping mold components.
- EDM: Electrical Discharge Machining (EDM) is useful for creating intricate details that traditional machining methods cannot achieve.
4. Assembly
The components are then meticulously assembled. This stage ensures that each part fits together perfectly to provide seamless operation in the final product.
5. Testing and Quality Assurance
Before the molds are deemed ready for production, rigorous testing is conducted to ensure they meet industry standards and client specifications. This includes:
- Dimensional Verification: Ensuring that all mold elements adhere to specified measurements.
- Functional Testing: Running trial productions to verify that the final products meet quality expectations.
Applications of Mold Manufacturing
The applications of molds span countless industries. Here are some notable examples:
1. Automotive Industry
Mold manufacturers provide sophisticated molds for components such as dashboards, panels, and exterior shells. The automotive industry relies heavily on precision and efficiency, making the role of mold manufacturers indispensable.
2. Consumer Goods
From kitchen appliances to electronics, the consumer goods sector utilizes molds for creating a variety of products. Mold manufacturers supply the tools necessary for producing items at scale while maintaining high durability and aesthetic appeal.
3. Medical Devices
In the medical field, molds are necessary for creating devices and equipment with strict regulatory standards. Mold manufacturers not only enhance the functionality of such devices but also ensure compliance with health and safety regulations.
4. Aerospace
The aerospace sector demands high precision and lightweight materials. Mold manufacturers play a crucial role in producing components that meet stringent industry standards, ensuring safety and reliability in air travel.
Choosing the Right Mold Manufacturer
When selecting a mold manufacturer, consider the following factors:
- Experience and Expertise: Look for manufacturers with a proven track record in your industry.
- Technological Capabilities: Ensure they utilize the latest technologies and methodologies for mold production.
- Quality Control: Investigate their quality assurance processes and certifications.
- Customer Support: A good manufacturer should offer robust customer service and support throughout the project lifecycle.
Future Trends in Mold Manufacturing
The mold manufacturing industry is continuously evolving, influenced by advancements in technology and changes in consumer demand. Some trends to watch include:
1. Automation and Robotics
The integration of automation in mold manufacturing enhances precision and efficiency. Automated systems can drastically reduce production times, yielding a higher output with consistent quality.
2. Additive Manufacturing
Additive manufacturing, or 3D printing, is making waves in mold production. This technology allows manufacturers to create complex mold geometries that were previously impossible with traditional methods.
3. Sustainability
As industries shift towards sustainability, mold manufacturers are adapting by using eco-friendly materials and energy-efficient processes. Reducing waste and improving recyclability in molds is becoming a priority.
4. Advanced Materials
New material innovations are set to revolutionize mold design. High-performance composites and lightweight materials can enhance the durability and functionality of molds, making them suitable for more demanding applications.
Conclusion
In conclusion, the role of a mold manufacturer is critical in the manufacturing landscape. Their work not only impacts product quality and operational efficiency but also drives innovation across multiple industries. As technology advances, the importance of skilled mold manufacturers will continue to grow, making them indispensable partners in crafting tomorrow's products. Visit deepmould.net to learn more about how a leading mold manufacturer can elevate your production capabilities.