Flange Hydraulic Fittings: A Comprehensive Guide to Quality and Performance
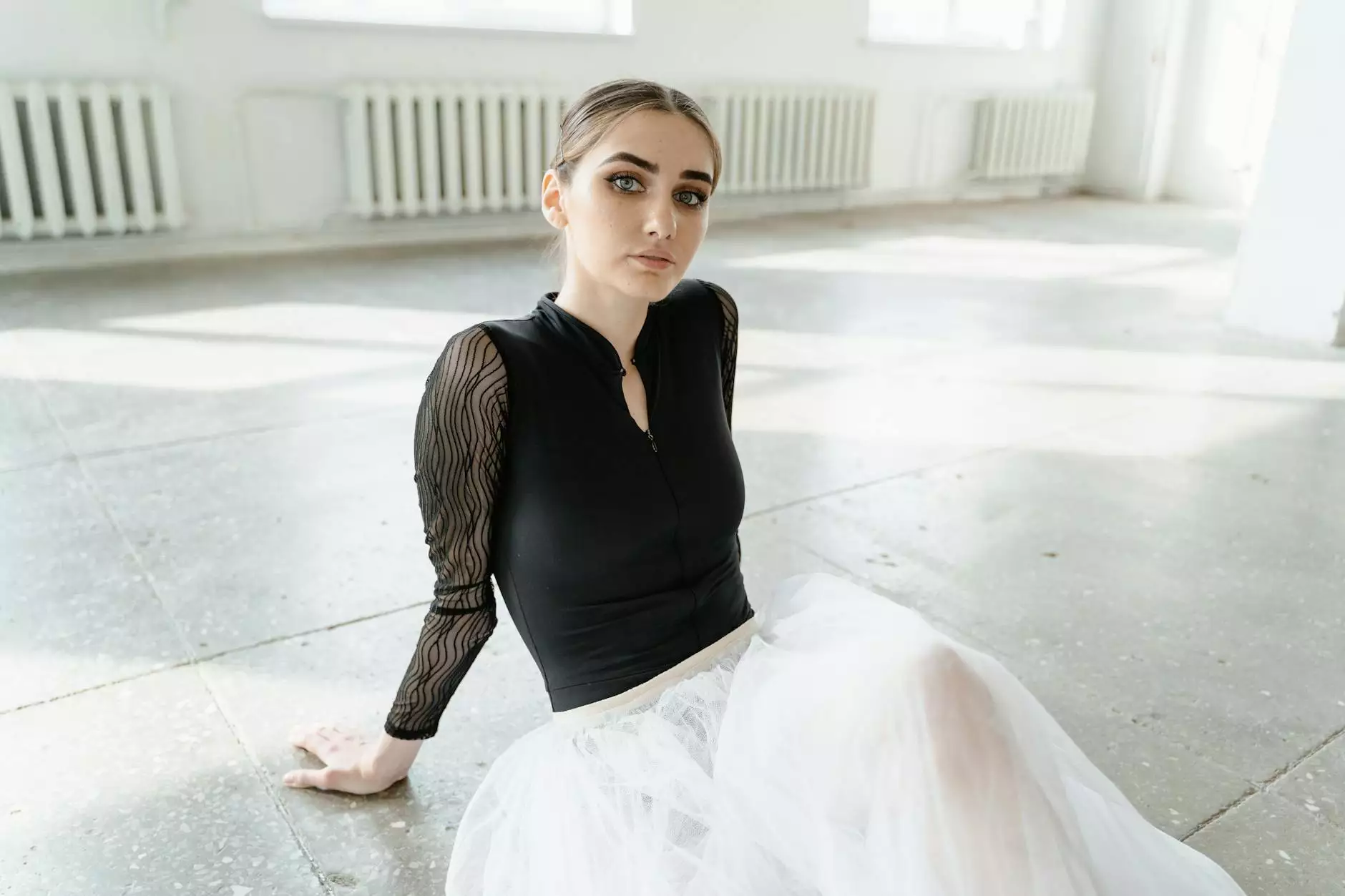
In the ever-evolving landscape of modern engineering and manufacturing, flange hydraulic fittings play a crucial role in ensuring the reliability and efficiency of hydraulic systems. This article provides an in-depth exploration of flange hydraulic fittings, their benefits, applications, and why they are an essential component in various industries. Whether you are a seasoned engineer or a newcomer to the world of hydraulics, understanding flange hydraulic fittings is key to optimizing your systems.
What Are Flange Hydraulic Fittings?
Flange hydraulic fittings are specialized connectors used in hydraulic systems to join pipes, hoses, and equipment while ensuring a tight and leak-proof seal. These fittings utilize flanges—flat pieces of metal with holes for bolts—allowing for easy installation and removal. They are commonly used in applications where high pressure and flow rates are present, making them ideal for various industrial settings.
Key Components of Flange Hydraulic Fittings
To fully appreciate the functionality of flange hydraulic fittings, it’s essential to understand their components:
- Flanges: The primary components that provide the connection point; they come in various sizes and pressure ratings.
- Bolts and Nuts: Used to secure the flanges together, ensuring a strong and tight seal.
- Gaskets: Placed between the flanges to prevent leakage and withstand high pressure.
- Material: Typically made from metal alloys, ensuring durability and resistance to corrosion.
Types of Flange Hydraulic Fittings
There are several types of flange hydraulic fittings, each designed for specific applications. Understanding these types is crucial for selecting the right fitting for your needs:
1. Flat Face Flange
Flat face flanges provide a flush surface, making them ideal for low-pressure applications where precise alignment is critical. They are commonly used in water and waste water management systems.
2. Raised Face Flange
Raised face flanges have an elevated surface, allowing for better sealing under high pressure. They are widely used in oil and gas applications, where reliability is paramount.
3. Lap Joint Flange
Lap joint flanges are used in conjunction with a stub end, allowing for easier alignment and disassembly. They are particularly beneficial in applications where frequent maintenance is required.
4. Blind Flange
Blind flanges are solid, with no openings, and are used to close the ends of pipelines. They are essential for system testing and maintenance.
Applications of Flange Hydraulic Fittings
The versatility of flange hydraulic fittings makes them applicable across numerous industries. Here are some common applications:
- Manufacturing: Used in hydraulic presses and machinery to ensure safe and efficient operations.
- Automotive: Essential in hydraulic braking systems, steering mechanisms, and other vehicle applications.
- Construction: Employed in heavy machinery such as excavators and loaders, providing reliable hydraulic connections.
- Mining: Critical in hydraulic systems for extracting minerals, where high pressure is necessary.
- Oil and Gas: Used in drilling rigs and refineries to manage high-pressure fluids effectively.
Benefits of Flange Hydraulic Fittings
Utilizing flange hydraulic fittings brings numerous advantages to hydraulic systems:
1. High Pressure Resistance
Flange hydraulic fittings are designed to withstand high-pressure environments, ensuring that fluids flow smoothly without leaks. This reliability is crucial for the safety and efficiency of hydraulic systems.
2. Easy Maintenance and Replacement
Due to their design, flange fittings can be easily installed and removed, facilitating maintenance and reducing downtime. This is particularly beneficial in industries where time is money.
3. Versatile Applications
Flange fittings can be used in a range of applications, from industrial machinery to automotive systems, making them a versatile choice for engineers.
4. Enhanced Sealing Capabilities
The incorporation of gaskets between flanges ensures superior sealing capabilities, preventing leaks and improving system integrity.
Choosing the Right Flange Hydraulic Fittings
Selecting the right flange hydraulic fittings is essential for optimal system performance. Here are some key considerations:
- Pressure Rating: Ensure the fitting’s pressure rating meets or exceeds the requirements of your hydraulic system.
- Material: Choose a material that is compatible with the fluid being used and can withstand the operational environment.
- Size: Proper sizing is crucial; ensure the fitting matches the diameter of your pipes or hoses for a secure fit.
- Standards Compliance: Check that the fittings comply with industry standards and regulations for safety and effectiveness.
Installation of Flange Hydraulic Fittings
Installing flange hydraulic fittings requires attention to detail to ensure a proper seal. Follow these steps for a successful installation:
- Preparation: Clean the surfaces of the flanges and ensure they are free from debris or damage.
- Gasket Placement: Position the gasket between the flanges, ensuring it is correctly aligned.
- Alignment: Align the flanges, making sure that the bolt holes are visible and accessible.
- Bolting: Insert bolts through the holes and hand-tighten them without excessive force.
- Tightening: Use a torque wrench to tighten the bolts in a criss-cross pattern to ensure even pressure distribution.
Maintenance Tips for Flange Hydraulic Fittings
To extend the lifespan of your flange hydraulic fittings, consider the following maintenance tips:
- Regular Inspections: Periodically check for leaks or signs of wear and tear.
- Fluid Checks: Monitor the hydraulic fluid for contamination which could affect the fittings.
- Seal Replacement: Replace gaskets as needed to maintain a tight seal and prevent leaks.
- Torque Verification: Re-check the torque settings periodically to ensure that the fittings remain secure.
Conclusion
In conclusion, flange hydraulic fittings are an indispensable component in hydraulic systems across various industries. Their ability to provide a robust and reliable connection under high-pressure conditions makes them the preferred choice for engineers and manufacturers. By understanding the types, applications, and maintenance practices associated with these fittings, you can optimize your hydraulic systems for enhanced performance and longevity.
For high-quality fittings for sale, visit fitsch.cn and discover a wide range of options tailored to meet your specific needs.