Architectural Wood Model Maker: Elevating Design Through Customization
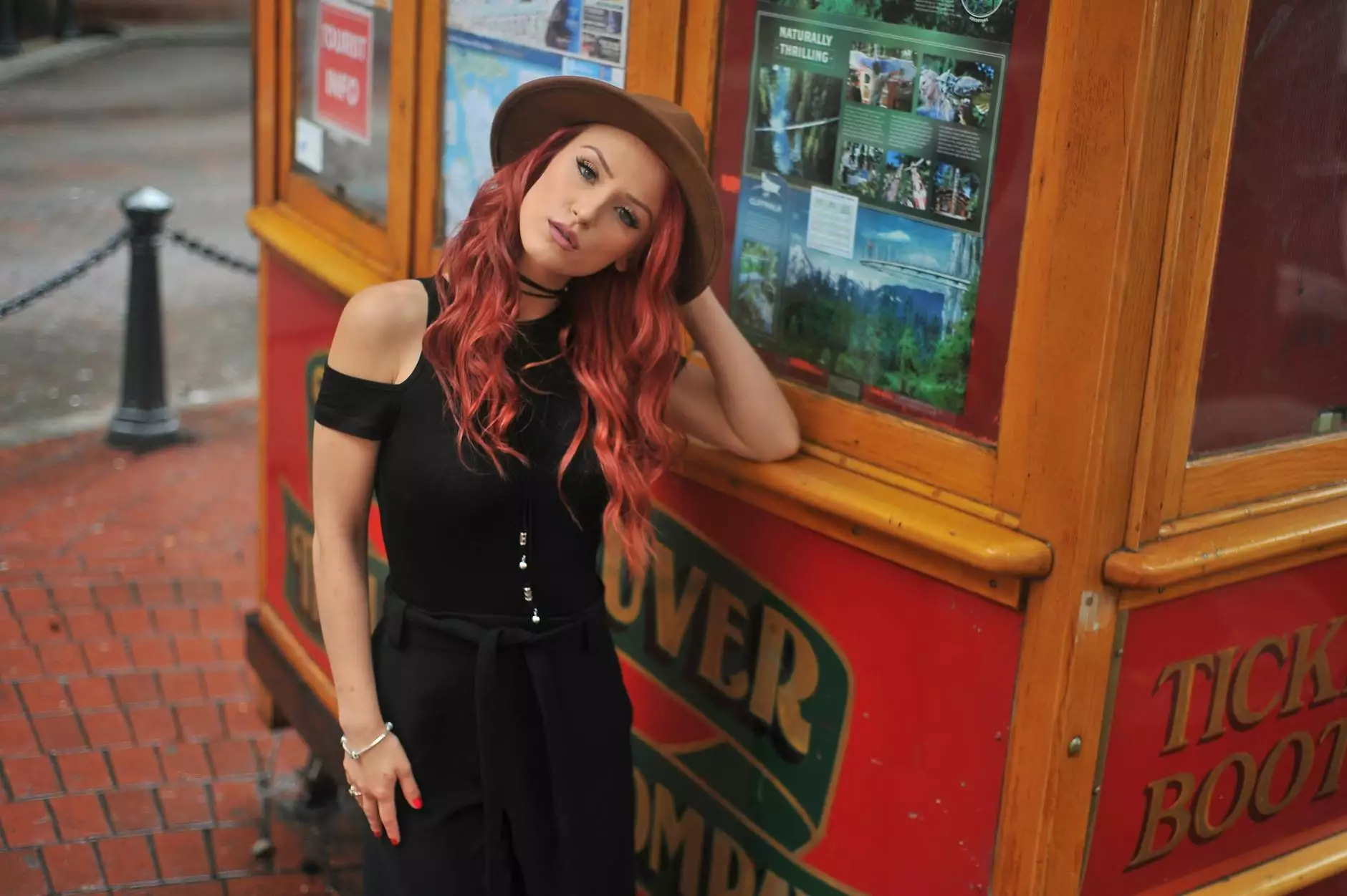
In the realm of architecture, the art of transforming conceptual designs into tangible representations is an essential task. This is where the expertise of an architectural wood model maker becomes invaluable. They provide clarity, enhance communication, and foster innovation by creating precise models that showcase architectural visions.
The Importance of Architectural Models
Architectural models play a crucial role in the architectural process. They serve multiple purposes, including:
- Visualization: Models allow stakeholders to better visualize the final product.
- Understanding: They help in grasping scale and proportions that can be difficult to depict in 2D drawings.
- Communication: Models act as effective communication tools between architects, clients, and contractors.
- Marketing: High-quality models enhance presentations for potential clients and investors.
What is an Architectural Wood Model Maker?
An architectural wood model maker specializes in the craftsmanship of creating detailed models from wood. This profession combines technical skill with artistic vision to produce models that accurately reflect the architectural intent. The process involves various stages, including:
1. Understanding the Design Intent
Before any physical model can be crafted, it is vital that the architectural wood model maker comprehends the design concept thoroughly. This involves collaborating closely with architects to grasp the nuances of their vision.
2. Material Selection
Wood is a favored material due to its workability, aesthetic appeal, and durability. An architectural wood model maker selects the appropriate type of wood, taking into account the project's requirements. Common choices include:
- Basswood: Lightweight and easy to cut, making it ideal for intricate details.
- Birch Plywood: Offers strength and a fine grain suitable for structural accuracy.
- Maple: Known for its durability and beautiful finish.
3. Crafting the Model
This stage requires a combination of precision and artistry. Techniques employed by an architectural wood model maker include:
- CNC Machining: Precise cutting and shaping using computer-controlled machines.
- Handcrafting: Utilizing traditional tools for unique, intricate designs.
- Assembly: Assembling the individual parts into a cohesive whole that accurately reflects the design.
4. Finishing Touches
After the model is assembled, the final stage involves detailing and finishing. This might include painting, staining, or varnishing to achieve a polished look, enhancing the model’s realism and aesthetic quality.
Why Choose Wood Models Over Other Materials?
While architectural models can be made from various materials, choosing wood has significant advantages:
- Natural Aesthetic: Wood models possess an organic beauty that resonates authenticity.
- Customizability: Wood can be easily molded and manipulated into a wide range of shapes.
- Eco-Friendly: Wood is often sourced sustainably, appealing to environmentally conscious clients.
Benefits of Hiring an Architectural Wood Model Maker
Engaging the services of a qualified architectural wood model maker can bring numerous benefits to architectural projects:
- Enhanced Communication: A physical model facilitates discussions among project stakeholders, minimizing misunderstandings.
- Effective Marketing Tools: Stunning wood models can captivate potential clients and help secure projects.
- Timely Feedback: Models enable quicker iterations and decisions during the design process.
Applications of Wood Models in Architecture
The applications of wood models extend across various architectural realms, including:
1. Conceptual Design Development
At the early stages of design, wood models help architects experiment with forms, shapes, and spatial configurations.
2. Client Presentations
Models serve as persuasive tools in client meetings, providing a clear representation of the architect's vision and building rapport.
3. Educational Purposes
Architectural schools often utilize wood models for teaching purposes, allowing students to understand design principles through hands-on experience.
4. Competitions and Exhibitions
In architecture competitions, a well-crafted wood model can set an entry apart, providing a captivating visualization that enhances the submission.
The Future of Architectural Wood Model Making
The future of architectural wood model making is promising, fueled by advances in technology and a renewed interest in craftsmanship. Some trends include:
- 3D Printing Integration: Combining traditional wood crafting with 3D printing technology to create hybrid models.
- Sustainability Focus: Increasing demand for eco-friendly practices and materials within model-making.
- Digital Models: The rise of digital presentations continues to shape the way models are used in projects.
Conclusion
In conclusion, the role of an architectural wood model maker is fundamental in bridging the gap between design and reality. Their expertise in crafting high-quality wood models enhances communication, fosters creativity, and supports architectural projects at every stage. By choosing to work with a skilled model maker, architects can ensure their visions are accurately realized and effectively communicated, leading to successful outcomes. Whether for presentations, client meetings, or educational purposes, the impact of custom wood models in architecture cannot be overstated.
Discover more about the transformative power of architectural models and elevate your next project with the craftsmanship of a professional architectural wood model maker. Visit us at architectural-model.com for more information.