Precision Plastic Injection Molding: A Comprehensive Exploration
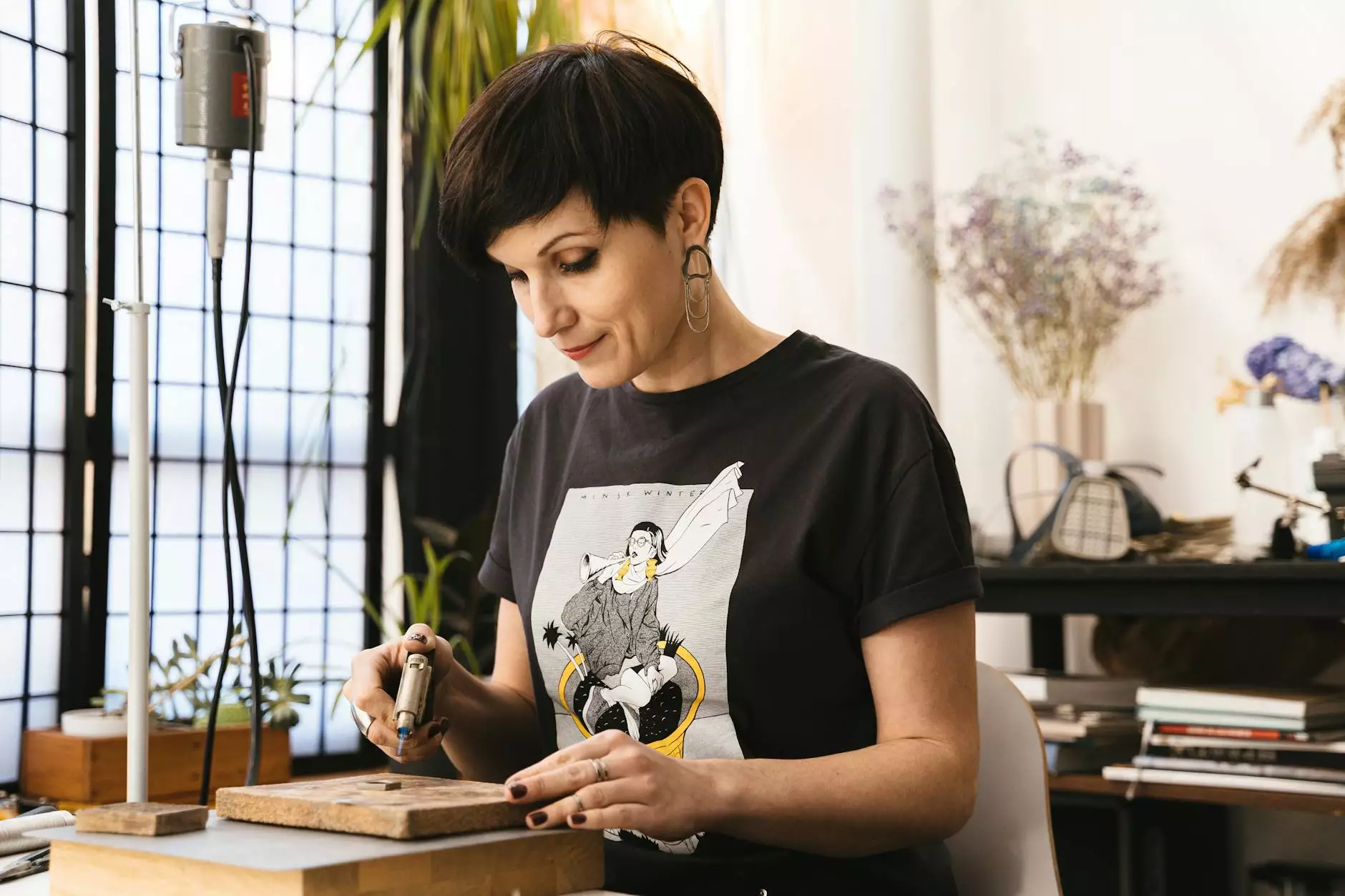
Understanding Precision Plastic Injection Molding
Precision plastic injection molding is a highly effective manufacturing process that involves creating parts by injecting molten plastic into a mold. This method is renowned for its ability to produce intricate parts with high accuracy and repeatability. Industries ranging from automotive to aerospace rely on this technique due to its efficiency and capability to produce complex geometries.
The Process of Precision Plastic Injection Molding
At its core, the precision plastic injection molding process can be broken down into several key phases:
- Material Selection: The process starts with choosing the right plastic material, which can significantly influence the outcome. Common materials include ABS, polycarbonate, and nylon.
- Mold Design: A well-designed mold is crucial. Molds are often crafted from steel or aluminum, and precision machining ensures that the mold can withstand high pressure while maintaining dimensional accuracy.
- Injection Phase: The plastic pellets are heated until they melt and are then injected into the mold cavity at high pressure. This phase is critical as it determines the fill time and the pressure applied.
- Cooling Phase: After injection, the plastic is allowed to cool and solidify. The cooling time is derived from the material properties and shape complexity.
- Mold Removal: Once cooled, the mold opens, and the finished plastic part is ejected. This step can also involve trimming excess material or runners.
This systematic approach ensures that every component meets the strict quality standards required in today's demanding industries.
Applications of Precision Plastic Injection Molding
Precision plastic injection molding is utilized in various fields. Some of the prominent applications include:
- Automotive Industry: Modular components such as dashboards, knobs, and panels.
- Consumer Electronics: Casings for phones, laptops, and chargers.
- Medical Devices: Precision components for devices like syringes, inhalers, and surgical tools.
- Toys and Games: Complex and vibrant figures that withstand rigorous play.
- Household Products: Everyday items like containers, bottles, and appliances.
The diversity of applications demonstrates the versatility and practicality of precision plastic injection molding.
Advantages of Precision Plastic Injection Molding
The benefits of choosing precision plastic injection molding for manufacturing processes are numerous:
- High Efficiency: Once the mold is created, mass production of parts can be achieved rapidly, reducing lead times significantly.
- Cost-Effectiveness: Although the initial mold cost can be high, the cost per unit decreases drastically when large volumes are produced.
- Minimized Waste: The process generates less scrap material compared to other manufacturing techniques.
- Complex Designs: It allows the production of intricate shapes and items that are otherwise challenging to make.
- Superior Consistency: Each piece produced is nearly identical, ensuring uniformity in quality.
Challenges in Precision Plastic Injection Molding
Despite its numerous benefits, there are challenges in the precision plastic injection molding process. These include:
- High Initial Costs: Designing and making a mold can require significant investment.
- Complex Setup: The process requires experience and expertise to set up properly, including adjustments to machine parameters.
- Material Limitations: Not all plastic types can be easily molded, limiting some applications.
- Maintenance of Molds: Molds can wear over time, necessitating repairs or replacements.
The Future of Precision Plastic Injection Molding
As technology continues to evolve, so does the field of precision plastic injection molding. Key trends shaping its future include:
- Automation: The integration of robotics and automated systems is set to enhance efficiency and reduce labor costs.
- Advanced Materials: Innovations in plastic materials are leading to more durable, lightweight, and eco-friendly options.
- Sustainability Practices: Manufacturers are increasingly looking at ways to reduce their environmental footprint, including better energy efficiency and recycling of materials.
- Digital Transformation: The use of IoT and data analysis can enhance quality control and predict maintenance needs.
These advancements underscore the potential growth and innovation within the manufacturing landscape.
Choosing the Right Precision Plastic Injection Molding Partner
Selecting the right partner for precision plastic injection molding is crucial for the success of your projects. When evaluating potential manufacturers, consider the following:
- Experience: Look for a company with a proven track record in delivering quality results in your specific industry.
- Technical Capabilities: Ensure they have the technology and equipment necessary to handle the intricacies of your designs.
- Quality Assurance: Investigate if they adhere to stringent quality standards and certifications.
- Customer Support: A reliable partner should offer excellent customer service throughout the collaboration process.
Conclusion: The Impact of Precision Plastic Injection Molding
In conclusion, precision plastic injection molding is a cornerstone in modern manufacturing, enabling industries to produce high-quality, complex plastic parts efficiently. Despite its challenges, the advantages offered by this process make it a preferred choice for many applications. As advancements in technology pave the way for improved practices and innovative materials, the future of injection molding appears promising, ensuring its role in shaping the products of tomorrow.