Unlocking the Potential of Precision Injection Plastic Moulds
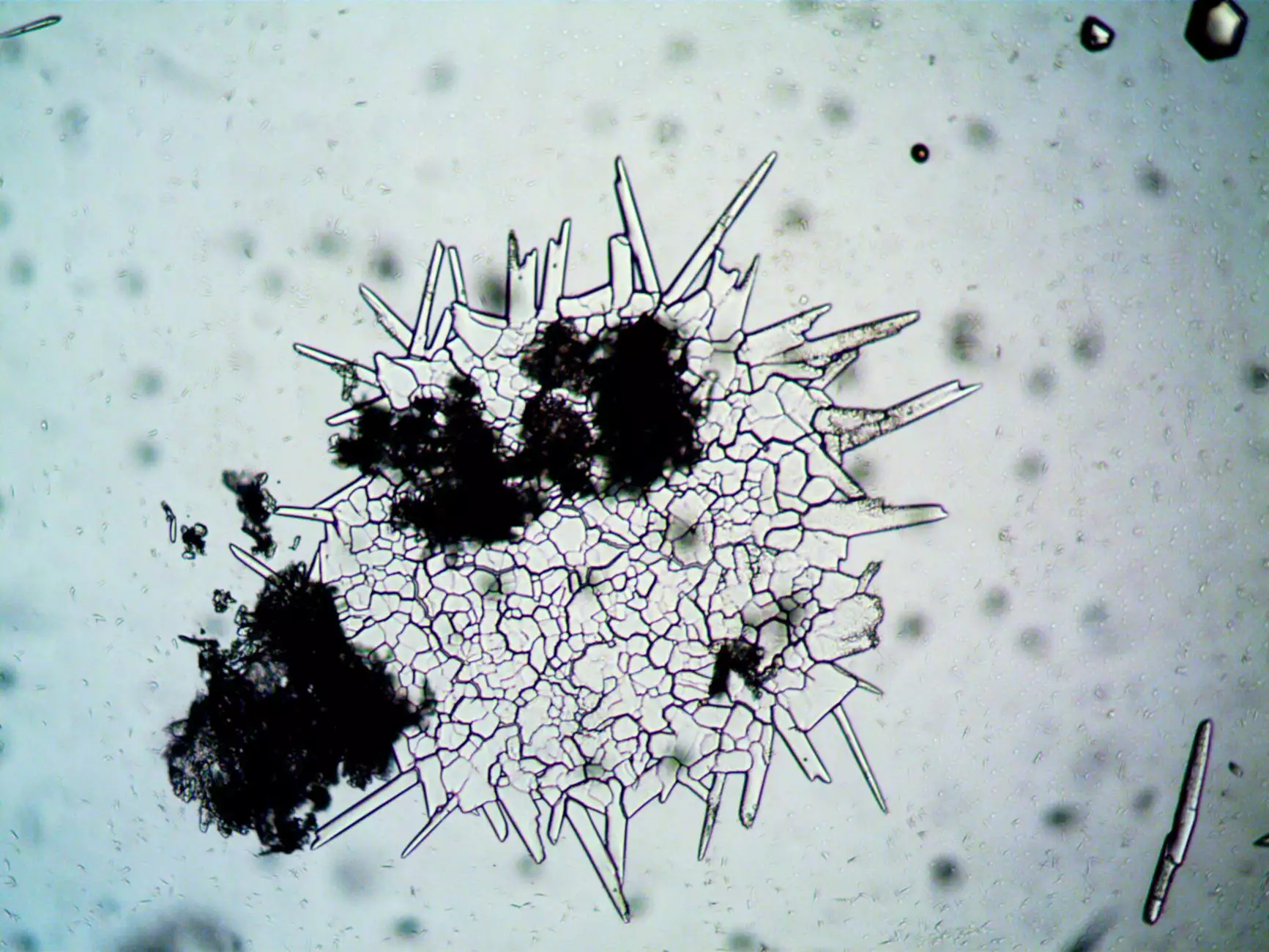
Precision injection plastic mould technology stands at the forefront of modern manufacturing, significantly enhancing product quality and efficiency. This article delves into the intricacies of precision injection moulding, elucidating its process, benefits, applications, and how it drives innovation in various industries.
What is Precision Injection Plastic Moulding?
Precision injection plastic moulding is a manufacturing process used to produce intricate plastic components with exact dimensions and high repeatability. The process involves injecting molten plastic into a specially designed mould, allowing for the creation of complex shapes and designs. This method is ideal for high-volume production, ensuring consistency and quality in every piece.
The Moulding Process Explained
The precision injection plastic mould process can be broken down into several key stages:
- Design and Prototyping: Initial designs are created using CAD software, allowing for precise calculations and modifications. Prototypes are often produced to evaluate the design's functionality.
- Mould Fabrication: Once a design is finalized, moulds are fabricated from high-quality materials, often steel or aluminum, using CNC machining or electrical discharge machining (EDM) to ensure precision.
- Injection: Molten plastic is injected into the mould at high pressure, filling the cavity and taking the shape of the mould.
- Cooling: The plastic is allowed to cool and solidify within the mould, which can take a few seconds to several minutes, depending on the material and part size.
- Demoulding: Once cooled, the mould opens, and the newly formed plastic part is ejected.
- Finishing: Final touches may include trimming excess material, surface treatment, and quality inspection to ensure every part meets the required specifications.
Benefits of Precision Injection Plastic Moulding
The adoption of precision injection plastic moulding offers a plethora of advantages:
- High Precision: The process produces parts with tight tolerances, ensuring quality and fitment.
- Efficiency: It allows for rapid production cycles, making it ideal for high-volume manufacturing.
- Cost-Effective: Although initial setup costs may be high, the cost per unit decreases significantly with higher production volumes.
- Material Variety: A wide range of thermoplastic materials can be utilized, allowing manufacturers to choose the best material for their specific application.
- Complex Geometries: The process facilitates the creation of intricate designs that would be challenging or impossible using other methods.
- Eco-Friendly Options: Many manufacturers are now using biodegradable and recyclable plastics in their production, reducing environmental impact.
Applications of Precision Injection Plastic Moulds
Precision injection plastic moulding serves an extensive range of industries, including:
1. Automotive Industry
Components such as dashboards, bumpers, and internal fixtures are often produced using precision injection moulding due to their need for high durability and precise fit.
2. Consumer Goods
Everyday items, from toys to kitchen gadgets, benefit from the precision and versatility of this moulding process.
3. Medical Devices
In the healthcare sector, precision injection moulding is critical for creating sterile, precise components such as syringes and medical instrument casings.
4. Electronics
From casings for gadgets to intricate internal components, precision moulding plays a vital role in the electronics industry.
5. Packaging Industry
Custom packaging solutions are often manufactured using precision moulding techniques to ensure that products are well-protected during shipping and display.
Choosing the Right Partner for Precision Injection Plastic Moulding
When selecting a manufacturing partner for precision injection moulding, consider the following factors:
- Experience: Look for a company with a proven track record and expertise in your industry.
- Technological Capability: Ensure that the partner employs advanced technology and adheres to international quality standards.
- Customization: The ability to create bespoke moulds and accommodate unique designs is crucial.
- Customer Support: Reliable partners provide ongoing support and communication throughout the project.
- Cost Structures: Understand the pricing models and aim for transparency in costs.
Conclusion
In conclusion, precision injection plastic mould technology is revolutionizing manufacturing across numerous sectors. Its efficient, cost-effective, and precise nature makes it the go-to solution for high-quality plastic components. By choosing the right partner, such as DeepMould, companies can harness this innovative technology to streamline their production processes and bring their ideas to life with remarkable accuracy.
As industries continue to evolve, the role of precision injection moulding will undoubtedly expand, providing even more opportunities for innovation and growth in manufacturing. By investing in this technology, businesses can ensure they remain competitive in an ever-changing market.